Blog
The Importance of Certificate of Analysis (COA) and Manufacturer’s Specification Data Sheet (MSDS)
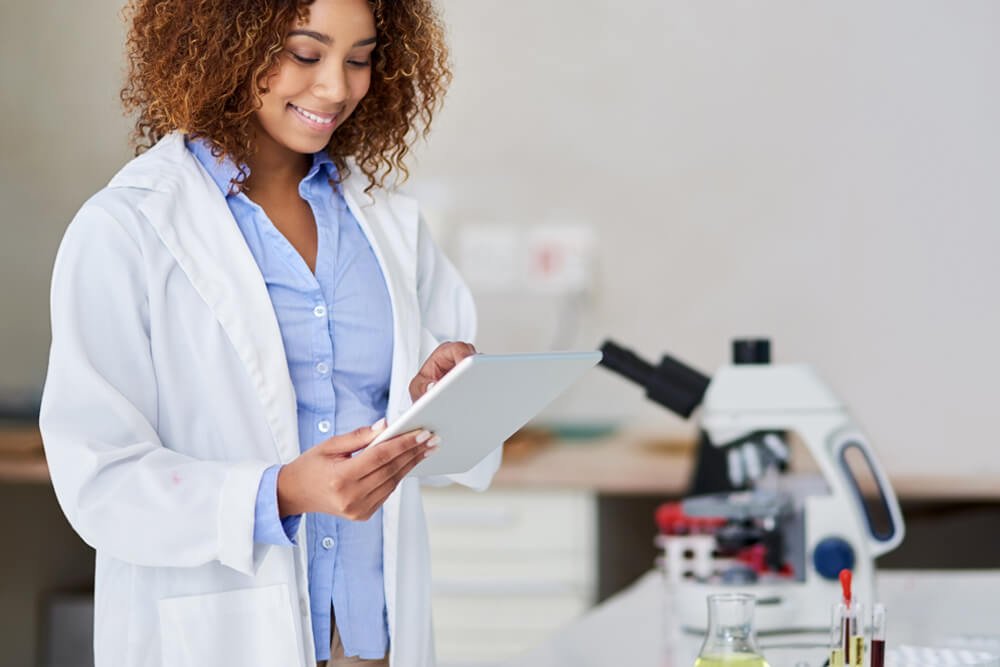
Both the Certificate of Analysis (COA) and Manufacturer’s Specification Data Sheet (MSDS) are essential documents that provide valuable information about the product’s composition, quality, and safety. They serve as a guarantee that the product meets the required standards and specifications.
The Certificate of Analysis (COA) is a document issued by an accredited laboratory that verifies the product’s quality and purity. It provides detailed information about the product’s chemical composition, physical properties, and any impurities or contaminants present. The COA is particularly important for industries such as pharmaceuticals and food production, where the slightest variation in quality can have significant consequences on the end product’s efficacy and safety.
The Manufacturer’s Specification Data Sheet (MSDS), on the other hand, provides comprehensive information about the product’s handling, storage, and safety precautions. It includes details about the product’s physical and chemical properties, potential hazards, and recommended safety measures. This document is crucial for industries where workers come into direct contact with the product, as it helps ensure their safety and prevent accidents or mishandling.
Having access to accurate and up-to-date COA and MSDS is not only important for the manufacturers and suppliers but also for the buyers. These documents allow them to make informed decisions about the products they purchase, ensuring that they meet their specific requirements and comply with the necessary regulations and standards.
Furthermore, the COA and MSDS play a vital role in product traceability and quality control. They provide a reference point for manufacturers and suppliers to track the product’s origin, manufacturing process, and quality control measures. In case of any issues or concerns, these documents serve as a valuable tool to investigate and resolve any potential problems.
In conclusion, the Certificate of Analysis (COA) and Manufacturer’s Specification Data Sheet (MSDS) are crucial documents that provide essential information about a product’s quality, safety, and compliance with industry standards. They are indispensable tools for both manufacturers and buyers, ensuring transparency, traceability, and adherence to regulations. By utilizing these documents, industries can maintain the highest standards of quality and safety, ultimately benefiting both the businesses and the end consumers.
What is a Certificate of Analysis (COA)?
A Certificate of Analysis (COA) is a document provided by the manufacturer or supplier of a product that verifies the product’s quality and compliance with specific standards. It serves as a guarantee that the product has been tested and meets the required specifications.
The COA typically includes information such as the product’s batch or lot number, manufacturing date, expiration date, and a detailed analysis of its composition. It may also include test results for various parameters, such as purity, potency, stability, and contaminants.
COAs are particularly important in industries where the quality and consistency of products are critical, such as pharmaceuticals, chemicals, and food and beverage. They provide assurance to customers that the product they are purchasing is of high quality and meets the necessary standards.
In the pharmaceutical industry, for example, COAs are essential for ensuring the safety and efficacy of drugs. They provide a comprehensive analysis of the drug’s composition, including the active ingredients and any impurities or contaminants present. This information is crucial for regulatory compliance and helps pharmaceutical companies maintain the highest quality standards.
Similarly, in the chemical industry, COAs play a vital role in ensuring that chemicals meet the required specifications for various applications. For instance, if a chemical is being used in the production of a specific type of plastic, the COA will outline the chemical’s composition and confirm that it meets the necessary purity and stability requirements. This helps manufacturers avoid potential issues such as product failure or safety hazards.
In the food and beverage industry, COAs are necessary to guarantee the quality and safety of products. They provide information on the product’s nutritional content, potential allergens, and any contaminants that may be present. This is particularly important for consumers with dietary restrictions or allergies, as they rely on accurate and detailed information to make informed choices about the products they consume.
COAs are not only beneficial for customers but also for manufacturers and suppliers. By providing a detailed analysis of their products, they can demonstrate their commitment to quality and regulatory compliance. This can help build trust with customers and differentiate their products in a competitive market.
In conclusion, a Certificate of Analysis (COA) is a crucial document that verifies the quality and compliance of a product with specific standards. It provides customers with assurance that the product has been tested and meets the necessary specifications. COAs are particularly important in industries where product quality and consistency are critical, such as pharmaceuticals, chemicals, and food and beverage. By providing detailed information on composition and test results, COAs help ensure the safety, efficacy, and quality of products, benefiting both customers and manufacturers.
5. Risk Mitigation:
COAs are essential for risk mitigation in various industries. For example, in the food and beverage industry, COAs can help identify potential allergens or contaminants that may pose a risk to consumers’ health. By providing detailed information about the product’s ingredients and testing results, COAs enable companies to take necessary precautions and prevent potential health issues.
6. Product Development and Improvement:
COAs are not only important for ensuring the quality of existing products but also for product development and improvement. By analyzing COAs, manufacturers can identify any variations or inconsistencies in the product’s composition or performance. This information can then be used to refine the manufacturing process, enhance product formulations, and ensure continuous improvement.
7. Legal Protection:
COAs can provide legal protection to manufacturers and suppliers. In case of any product-related issues or disputes, having comprehensive COAs can serve as evidence of compliance with quality standards and regulatory requirements. This can help protect the reputation and integrity of the company and minimize potential legal liabilities.
8. Customer Confidence:
By providing COAs, companies can instill confidence in their customers. Customers value transparency and knowing that the products they purchase have been thoroughly tested and meet the required standards. Having COAs readily available can help build trust and loyalty among customers, leading to increased customer satisfaction and repeat business.
9. Supply Chain Management:
COAs play a crucial role in supply chain management. They provide a standardized format for documenting and communicating important product information between manufacturers, suppliers, and customers. This helps ensure that all parties involved in the supply chain are well-informed about the product’s quality, composition, and compliance, enabling smooth operations and efficient decision-making.
10. International Trade:
COAs are particularly important in international trade, where products may need to comply with different regulatory standards and requirements. By providing COAs that demonstrate compliance with specific international standards, manufacturers can facilitate trade and ensure that their products meet the necessary import/export regulations of different countries.
Overall, COAs are a critical component of product quality management, regulatory compliance, and customer satisfaction. They provide valuable information that enables companies to ensure consistent product quality, mitigate risks, protect their legal interests, and maintain transparency and accountability throughout the supply chain.
What is a Manufacturer’s Specification Data Sheet (MSDS)?
A Manufacturer’s Specification Data Sheet (MSDS), also known as a Safety Data Sheet (SDS), is a document that provides detailed information about the hazards, handling, storage, and emergency procedures related to a specific product.
The MSDS typically includes information such as the product’s physical and chemical properties, potential hazards, recommended storage conditions, first aid measures, and disposal instructions. It also provides guidance on how to safely handle and use the product to minimize the risk of accidents or injuries.
MSDSs are commonly used in industries where the products used or produced can pose potential health or safety risks, such as chemicals, cleaning agents, and hazardous materials.
These sheets are an essential component of workplace safety programs as they provide crucial information to workers and employers about the potential hazards associated with the products they handle. By understanding the hazards and proper handling procedures outlined in the MSDS, workers can take appropriate precautions to protect themselves and others from harm.
Furthermore, MSDSs play a vital role in emergency preparedness. In the event of a spill, leak, or other hazardous situation, the MSDS provides guidance on how to respond and mitigate the risks effectively. This information can be crucial in preventing accidents, minimizing the impact of incidents, and ensuring the safety of both personnel and the environment.
Regulatory agencies, such as the Occupational Safety and Health Administration (OSHA) in the United States, require manufacturers to provide MSDSs for certain products. These regulations aim to promote workplace safety and ensure that employees have access to the necessary information to protect themselves from potential hazards.
It is important for employers to maintain up-to-date MSDSs for all hazardous substances used or produced in their workplace. This includes regularly reviewing and updating the sheets as needed to reflect any changes in the product’s composition, hazards, or recommended safety precautions.
In addition to being a legal requirement, MSDSs also serve as valuable resources for training programs and safety awareness campaigns. By familiarizing themselves with the information provided in the sheets, employees can make informed decisions about the safe handling and use of products, reducing the likelihood of accidents or injuries.
In conclusion, a Manufacturer’s Specification Data Sheet (MSDS) is a comprehensive document that contains vital information about the hazards, handling, storage, and emergency procedures associated with a specific product. It is an essential tool for promoting workplace safety, ensuring regulatory compliance, and empowering employees to make informed decisions regarding product use and handling.
5. Employee Training and Education:
MSDSs play a crucial role in employee training and education. By providing comprehensive information about the hazards associated with a product, MSDSs enable employers to educate their employees on the proper handling and use of potentially dangerous substances. This includes training on the use of personal protective equipment, emergency response procedures, and safe storage practices.
6. Risk Assessment:
MSDSs are an essential tool for conducting risk assessments in the workplace. By reviewing the information provided in the MSDS, employers can identify potential hazards and evaluate the associated risks. This allows them to implement appropriate control measures to minimize the likelihood of accidents or injuries.
7. Supplier Communication:
MSDSs facilitate communication between suppliers and end-users. When purchasing a product, companies can request the MSDS from the supplier, ensuring that they have access to all the necessary information to handle the product safely. Additionally, suppliers can use MSDSs to inform customers about any changes or updates to the product’s hazards or handling instructions.
8. Environmental Protection:
MSDSs also provide information on the environmental impact of a product. They outline proper disposal methods and any potential risks to the environment. This enables companies to take appropriate measures to minimize their environmental footprint and comply with environmental regulations.
9. Record Keeping:
MSDSs serve as an essential record-keeping tool. Companies are required to maintain MSDSs for all hazardous substances used in their workplace. These records help demonstrate compliance with regulatory requirements and can be valuable in the event of an inspection or audit.
10. Continual Improvement:
By regularly reviewing and updating MSDSs, companies can continually improve their safety practices. New information about a product’s hazards or safer handling methods can be incorporated into the MSDS, ensuring that employees have the most up-to-date information to protect themselves and others.
In conclusion, MSDSs are vital documents that provide critical information about the hazards associated with products. They play a crucial role in ensuring the safe handling, storage, and use of potentially dangerous substances, as well as facilitating regulatory compliance, employee training, and environmental protection.